Hunterweldz: An In-Depth Guide to Advanced Welding Techniques and Equipment
Introduction
Hunterweldz is a leading provider of advanced welding technologies and equipment, renowned for its commitment to innovation and quality. This comprehensive guide delves into the world of Hunterweldz, exploring the latest techniques, products, and industry trends.
Innovative Welding Techniques
1. Laser Welding
Laser welding utilizes a high-intensity laser beam to fuse materials, resulting in precision welds with minimal heat distortion. According to the American Welding Society (AWS), laser welding is increasingly adopted in automotive, electronics, and aerospace industries.

2. Electron Beam Welding (EBW)
In EBW, a focused electron beam is directed at the workpiece, generating intense heat that welds materials with exceptional precision. EBW is widely used in high-performance applications, such as jet engines and surgical implants.
3. Resistance Welding
Resistance welding utilizes pressure and electrical current to bond metals when they come into contact. Common resistance welding methods include spot welding, seam welding, and projection welding. The automotive industry extensively employs resistance welding for joining vehicle components.

Hunterweldz Equipment and Technologies
Hunterweldz offers a wide range of welding equipment, including:
-
Hypertherm Plasma Cutters: State-of-the-art plasma cutters that provide precise and efficient cutting of various materials.
-
Miller Welding Machines: Industrial-grade welding machines that deliver superior performance and reliability.
-
Lincoln Electric Welders: Renowned for their advanced features and rugged construction, suitable for demanding welding applications.
In addition, Hunterweldz offers specialized welding solutions, such as:
-
Automated Welding Systems: Robotic and CNC-controlled welding systems for increased productivity and precision.
-
Multi-Process Welders: Versatile welding machines capable of performing various welding processes, such as MIG, TIG, and stick welding.
-
Portable Welding Equipment: Lightweight and portable welding machines for mobile applications and field repairs.
Industry Trends and Applications
Welding is essential in various industries, including:
-
Automotive: Joining vehicle components, including body panels, chassis, and exhaust systems.
-
Aerospace: Manufacturing aircraft components, spacecraft, and satellites that require high-strength and lightweight welds.
-
Construction: Fabricating steel structures, bridges, and buildings.
-
Medical: Producing medical devices, implants, and surgical instruments with precision and cleanliness.
Benefits of Hunterweldz Equipment and Services
Choosing Hunterweldz products and services offers several benefits:
-
Advanced Technology: Hunterweldz equipment incorporates the latest welding technologies for superior performance and efficiency.
-
Quality Assurance: All Hunterweldz products meet rigorous industry standards, ensuring reliability and durability.
-
Expert Support: Hunterweldz provides comprehensive technical support and training to assist customers in optimizing their welding operations.
-
Custom Solutions: Hunterweldz offers customized welding solutions to meet specific application requirements.
How to Improve Welding Performance
To enhance welding performance, consider the following strategies:
-
Use proper welding techniques: Learn and apply the correct welding techniques for the specific materials and processes involved.
-
Select the right welding equipment: Choose welding machines and consumables compatible with the materials and applications.
-
Practice regularly: Regular welding practice builds muscle memory and improves hand-eye coordination.
-
Maintain welding equipment: Regularly inspect and calibrate welding equipment to ensure optimal performance.
-
Consider professional training: Enroll in welding courses or workshops to acquire advanced welding skills.
Step-by-Step Approach to Welding with Hunterweldz Equipment
Step 1: Preparation
- Gather necessary materials and equipment.
- Prepare the workpiece by cleaning and removing any impurities.
- Select the appropriate welding process and consumables.
Step 2: Equipment Setup
- Set up the welding machine according to the manufacturer's instructions.
- Connect the welding torch and ground cable.
- Adjust the welding parameters (amperage, voltage, etc.) as per the recommended settings.
Step 3: Welding
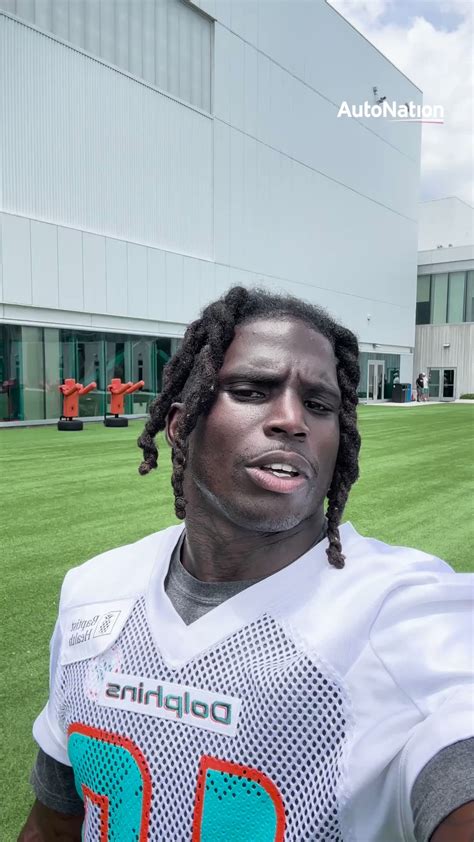
- Position the welding torch at the correct angle and distance from the workpiece.
- Start the welding process and maintain a steady hand and consistent speed.
- Monitor the weld pool and make adjustments as needed.
Step 4: Post-Welding
- Allow the weld to cool completely.
- Clean any slag or spatter from the weld joint.
- Inspect the weld for quality and performance.
Frequently Asked Questions (FAQs)
1. What are the key factors to consider when selecting a welding machine?
- Power output (amperage)
- Welding process (MIG, TIG, etc.)
- Duty cycle
- Portability
- Brand reputation
2. How often should welding equipment be serviced?
- Regular inspections and minor tune-ups are recommended every 6-12 months.
- Major servicing intervals may vary depending on equipment usage and manufacturer's recommendations.
3. What are the different types of welding consumables?
- Welding electrodes (stick welding)
- Welding wire (MIG and TIG welding)
- Flux and shielding gases
- Weld backing tape
4. What safety precautions should be taken when welding?
- Wear proper protective clothing (welding helmet, gloves, etc.)
- Ensure adequate ventilation in the welding area.
- Keep the welding environment free of flammable materials.
5. What are the welding processes best suited for beginners?
- Stick welding (SMAW)
- MIG welding (GMAW)
6. How can I improve my welding skills?
- Practice regularly
- Study welding theory and techniques
- Seek guidance from experienced welders or professionals
Call to Action
Embark on your welding journey with Hunterweldz. Contact